Learn Essential Hazard Awareness Skills for OSHA-Compliant Safety
Written by Staff Writer
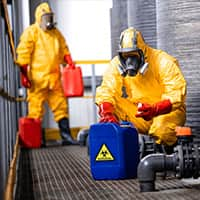
Imagine a workplace where everyone can identify and manage potential dangers. Whether on construction sites, warehouse floors or office premises, recognizing risks before they escalate ensures a productive day and prevents costly mishaps.
This proactive approach aligns with OSHA standards, making such instruction not just advisable but often mandatory. For organizations dedicated to employee well-being, regulatory adherence and public protection, thorough education on risk identification is crucial.
OSHA Education Center offers premier programs focused on identifying and preventing dangers. By adhering to federal and state guidelines, it equips workers and employers with the necessary skills to foster compliant environments. This article dives into essential aspects of risk recognition and highlights key educational modules, including DOT HAZMAT, hazard communication and understanding chemical hazards courses.
Why Risk Recognition Matters
Everyday tasks can conceal significant threats until an incident occurs. Proactively identifying risks helps workers minimize or eliminate potential issues, whether they involve chemicals, physical elements or environmental factors. Benefits include:
- Employee Well-Being: Workers remain secure when they can spot potential threats.
- Regulatory Compliance: OSHA regulations and other guidelines often mandate instruction on risk identification.
- Cost Reduction: Fewer injuries and damages lead to reduced insurance claims, fines and legal issues.
- Productivity Boost: A secure environment enhances morale and efficiency.
In sectors dealing with chemicals, heavy machinery or transportation, vigilance is the first step in managing risk. Whether overseeing a forklift operator or a team handling hazardous shipments, education in risk recognition fosters a culture of proactive vigilance.
Core Elements of Prevention
Effective risk mitigation involves more than just reviewing labels or manuals. Key components include:
- Identifying Risks: Recognizing different types of threats — chemical, biological or physical — and their common locations.
- Evaluating Severity: Assessing the likelihood and potential impact of each risk.
- Implementing Controls: Establishing procedures, using protective equipment and adopting best practices to address identified threats.
- Clear Communication: Ensuring all personnel understand warning signs and appropriate responses.
- Ongoing Monitoring: Regularly reviewing procedures and updating staff on new threats or regulations.
A structured, OSHA-aligned approach cultivates a robust culture of safety. Beyond mere compliance, it encourages continuous improvement and keeps employees engaged in maintaining secure practices throughout their careers.
Who Benefits from These Programs?
Organizations of all sizes — from large manufacturers to office-based businesses — can benefit from risk recognition programs. Common environments include:
- Manufacturing and Industry: Handling heavy machinery, chemical processes and production lines involves constant risks.
- Transport and Logistics: Employees managing loading, packing or shipping regulated materials encounter daily threats addressed by DOT guidelines.
- Healthcare and Laboratories: Concerns include chemical exposure and biological agents in medical and research settings.
- Construction: Teams deal with electrical threats, powerful substances and must comply with evolving OSHA standards.
- Office Environments: Even low-risk areas can present issues like cleaning agents, improper wiring or ergonomic challenges.
New hires and employees with changing responsibilities should complete relevant courses within 90 days. Refresher sessions are typically required every one to three years, ensuring ongoing vigilance and preparedness.
Compliance Essentials: Regulations and Recurrent Courses
OSHA requires employers to maintain workplaces free from recognized dangers. For dangerous materials, the Department of Transportation (DOT) enforces standards under 49 CFR 172.704 Subpart H (HM-181), which include:
- Initial Sessions: Completion within 90 days of hiring or job changes involving regulated substances.
- Recurrent Instruction: Employees must retake courses every three years.
- Documentation: Maintaining records (certificates, course outlines) for potential audits.
Similarly, the Hazard Communication Standard mandates informing workers about chemical risks, updated labels and changes to safety data sheets (SDS). The Globally Harmonized System (GHS) has redefined threat classification and labeling worldwide, emphasizing consistent communication and standardized data.
Integrating regular risk recognition sessions into routine protocols helps organizations avoid compliance issues and demonstrate genuine concern for employee welfare. Staying informed bridges prevention gaps, reducing potential harm and associated costs.
Enroll Now: Protect Your Team and Your Business
Investing in comprehensive risk recognition programs offers widespread benefits. By addressing potential issues early, employers limit exposure, maintain regulatory alignment and cultivate a responsible culture that benefits both workers and the community.
OSHA Education Center provides flexible, fully online courses that meet essential federal and state requirements. Options include foundational classes like DOT HAZMAT Transportation: Basic General Awareness, comprehensive programs such as DOT Hazardous Materials Transportation, specialized certificates in GHS & hazard communication and understanding chemical hazards.
Ready to enhance workplace security? Enroll in one of our courses today and equip your team with the knowledge needed to stay secure.